IoT Solutions
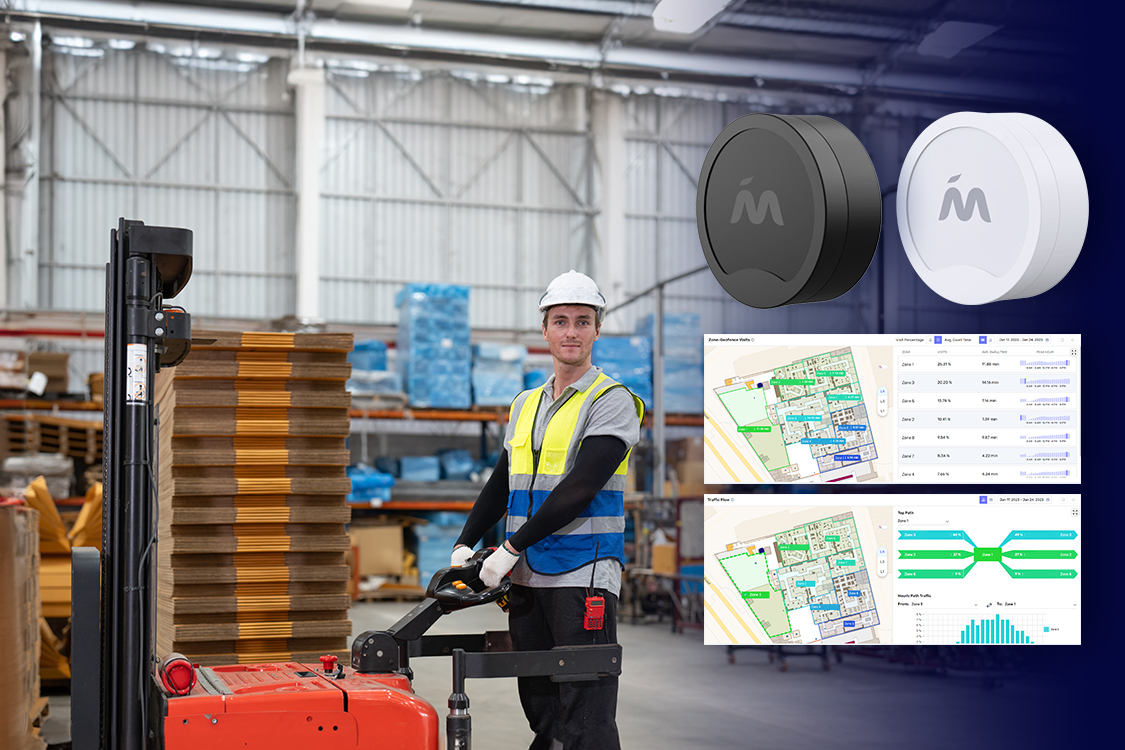
Dealing with maintenance operations and unexpected equipment breakdowns? You’re not alone! A report found that 72 large multinational industrial and manufacturing companies lose an average of 323 hours of production per year due to unplanned downtime, amounting to $172 million per plant. This situation is not unique, many others face similar problems. Efficiency drops and money is wasted when production runs behind schedule, creating a vicious cycle that affects a company’s growth and reliability. The answer is preventive maintenance. Preventative maintenance is the process of identifying inconsistent equipment performance and fixing it before it leads to disasters. In this blog we will explore five essential equipment management system strategies to enhance your current procedures and implement new ones for better operations.
Overview
In today’s competitive industrial landscape, having a reliable equipment management system is no longer optional—it’s essential. From manufacturing to healthcare, businesses face increasing pressure to minimize downtime, extend asset lifespans and cut operational costs. This blog explores five proven strategies to enhance your equipment management process, improve overall performance and overcome common equipment management challenges. Whether you’re dealing with reactive maintenance or seeking to digitize your asset tracking, these insights will help you boost efficiency and ROI. Dive in to discover practical equipment management tips, case studies and cutting-edge solutions to help your organization stay ahead in 2024 and beyond.
Why Equipment Management Matters in 2024
Missed deadlines, unhappy clients and lost revenue are equivalent to downtime. For example, according to Forbes, manufacturers experience approximately 800 hours of lost time at work and lose about $50 billion annually as a result of equipment breakdowns. The need to apply these five key strategies is very important for competitive edge maintenance.


1. Data-Driven Decisions: The Foundation
Managing equipment without data is like driving with your eyes closed. Leveraging data offers crucial insights into asset performance, facilitating better decision-making.
Harnessing Data to Drive Strategies
Don’t just collect data—use it. Optimize maintenance schedules, allocate assets effectively, and make informed decisions about future equipment purchases based on real-time information. Knowing the location, usage patterns, and maintenance history of each item dramatically improves efficiency and profitability.
As per the statistics, the global market for asset tracking systems is booming. It was $14.3 billion in 2022 and is projected to reach $34.5 billion by 2032.
Industry-Specific Examples:
- Healthcare: Effective asset tracking solutions ensure medical equipment is available, reducing search time.
- Manufacturing: Data analytics predicts machinery failures, minimizing unplanned downtime.
Tips:
- Implement asset tracking systems (like Mapsted’s IoT Tags) for real-time data.
- Use data analytics tools to analyze performance trends.
- Create data-driven maintenance schedules to predict and prevent failures.
2. Proactive Maintenance: A Strategic Shift
You wouldn’t wait for your car to break down before servicing it. Apply the same logic to your equipment. Proactive maintenance prevents costly downtime. Studies show that inadequate equipment maintenance system is a primary reason behind project overruns in this industry, contributing to nearly half the costs. It’s crucial to understand the different types of maintenance:
Types of Maintenance & Best Practices
- Reactive Maintenance (Run to Failure): This involves waiting for equipment to fail before fixing it. While tempting in terms of immediate costs, it’s significantly more expensive in the long run.
- Preventive Maintenance (Scheduled/Planned): This involves following a strict routine for inspections, cleaning, and component replacement at set intervals. These intervals are often dictated by manufacturers or industry standards. The benefit? It reduces the likelihood of unexpected breakdowns.
- Proactive Maintenance (Predictive/Condition-Based): This uses data analysis and condition-monitoring technologies like sensors to predict potential failures before they occur. It’s about staying ahead of the curve, minimizing downtime and maximizing productivity.
Industry-Specific Examples:
- Construction: Regular maintenance of heavy machinery avoids project delays.
- Manufacturing: Predictive maintenance reduces unexpected production stops.
Actionable Tips:
- Develop a preventive maintenance schedule based on manufacturer recommendations.
- Invest in condition-monitoring sensors to detect early wear and tear.
- Use predictive maintenance software to anticipate and prevent failures.
3. Training & Certification: Empowering Your Team
Even the most advanced equipment is useless without a trained team. Training is essential, especially with increasingly complex technology.
The Importance of Upskilling
Invest in your employees by providing access to high-quality training programs on equipment operation, maintenance, and safety. Continuous learning is key to maximizing equipment performance.
Actionable Tips:
- Offer comprehensive training programs on equipment use, maintenance, and safety.
- Conduct regular refresher courses to reinforce best practices.
- Utilize simulation training for complex equipment.
4. Investing Wisely: Total Cost of Ownership
Don’t just consider the initial price tag. Calculating Total Cost of Ownership (TCO) is essential for making informed purchasing decisions.
Understanding Total Cost of Ownership
TCO includes all expenses associated with equipment throughout its lifespan, providing a more accurate picture of its value.
Actionable Tips:
- Evaluate all costs: purchase price, maintenance, operation, and disposal.
- Compare TCO across different options to select the best equipment.
- Consider potential downtime costs and productivity impacts.
5. Technology as an Ally: Choosing the Right Software Solutions
With numerous software options, selecting the right equipment management system software can be challenging. Research thoroughly and choose software that meets your specific needs.
Features of Equipment Management System Software & Industry Use Cases
Specialized software streamlines equipment asset tracker and overall equipment management.
Specific Examples:
- Airports: Inventory management software increases efficiency and improves the traveller experience.
- Healthcare: Asset tracking systems ensure critical medical equipment is readily available.
Actionable Tips:
- Identify software with real-time tracking and data analysis capabilities.
- Choose platforms with intuitive interfaces and strong support.
- Ensure the software integrates seamlessly with your existing systems.
- Mapsted IoT Tags offer superior accuracy and extended battery life for equipment asset tracker and asset management
- Mapsted Badge for personnel monitoring improves operational efficiency and safety.
- Mapsted Flow for real-time heat mapping optimizes space utilization and crowd management.
Real-World Case Studies
Equipment management tools and solutions are widely used across various industries. Here are some real-world case studies of organizations that have successfully incorporated equipment management solutions:
1. Goldcorp’s Éléonore Mine
Goldcorp grappled with managing machinery and employees in the remote Éléonore mine located in northern Quebec, Canada. They implemented a smart mining solution that involved real-time tracking of equipment, predictive maintenance and remote monitoring. This led to a 20% decrease in equipment downtime and reduced maintenance costs by 15%; overall production increased by 10%.
2. Rio Tinto
Rio Tinto sought to enhance its mining activities. They utilized self-driving haul trucks as well as monitoring real-time data. As a result, there was an improvement of 15% in efficiency and cost reduction at 10%.
3. Boliden’s Aitik Mine
Boliden wanted to improve efficiency and sustainability at the Aitik open-pit copper mine. For this reason, they introduced a GPS-enabled fleet management system that included real-time analytics on data and machine learning algorithms.
The outcome of these plans resulted in a productivity increase of about 15%, fuel consumption drop by around 10%, and maintenance cost fall by roughly 5%.
4. Newcrest Mining’s Lihir Mine
Newcrest Mining had the challenge of dealing with an aging fleet at Lihir mine located in Papua New Guinea. They implemented a condition monitoring system that uses sensors and machine learning to forecast failures accurately thus optimizing maintenance activities. Among these are unplanned downtime which is reduced by about 25%, maintenance costs goes down by approximately 10% while equipment availability falls slightly less than 5%.
Conclusion
These five key elements: leveraging data, adopting proactive maintenance, investing in training, understanding TCO, and selecting the right software can transform your equipment management. While implementation requires effort, the long-term benefits are substantial.Remember, effective equipment management is an ongoing process. Regularly assess your practices, adapt to new technologies, and value your team’s expertise. By making informed decisions, you’ll enhance efficiency, reduce costs, and achieve long-term success. Embrace these strategies and watch your business thrive!
If you would like to discover more about the inner workings of effective tracking solutions or personnel monitoring technology and its exclusive benefits, feel free to check out our blog on Asset Tracking: How It Works & Its Benefits. And watch our videos showcasing our technology: Empower Your Business With Advanced Location-Based Analytics Solutions and Maximize Operational Efficiencies and Employee Satisfaction With Location-Based Technology. Feel free to contact us for more details and information.
Frequently Asked Questions
Q1. What are the advantages of equipment tracking systems?
Ans. Equipment tracking systems provide a number of benefits including better asset visibility, reduced equipment loss, optimized usage, simplified servicing and improved safety.
Q2. How do I select the right equipment management software for my company?
Ans. Consider factors such as your specialization, size of the fleet you are managing, money at hand and the key features that you want. Look around for different options, read reviews and even ask for a demo before settling on one.
Q3. What are some typical equipment management errors to avoid?
Ans. The key mistakes in this field include: lack of regular maintenance practices; poor inventory control; lack of sufficient employees’ training; underutilization of technology in this area.
Q4. Are advanced equipment management technologies like AI and IoT worth investing in?
Ans. Certainly! With their predictive maintenance capabilities, real-time monitoring functions and data-based insights into operations these technologies offer great opportunities to become more effective and reduce costs.
Q5. In what ways can I foster a strong safety culture surrounding equipment management within my organization?
Ans. Openly discuss safety concerns; improve staff competency through regular training sessions on safety issues; carry out health checks to verify whether organizational infrastructure complies with all current norms or not; acknowledge any efforts made by workers in realizing safe workplaces.
Q6. What is an equipment management system and why is it important?
Ans. An equipment management system is a digital platform used to monitor, track and maintain physical assets across their lifecycle. It helps businesses reduce downtime, extend asset life and cut operational costs—making it essential for industries relying on high-value equipment.
Q7. What are the key challenges of equipment management across industries?
Ans. Common equipment management challenges include poor maintenance tracking, lack of real-time visibility, manual data errors and unplanned downtime. Implementing digital solutions helps streamline the equipment management process and address these pain points effectively.
Q8. How can businesses improve company equipment management practices?
Ans. To improve company equipment management, businesses should adopt proactive maintenance strategies, train staff, track assets using IoT tags and invest in robust equipment maintenance management software. These steps ensure smoother operations and lower repair costs.
Q9. What are the essential elements of an effective equipment management process?
Ans. Core equipment management elements include real-time asset tracking, predictive maintenance, lifecycle documentation, personnel training and cost analysis. These form the foundation of a successful equipment information management strategy that boosts efficiency.
Q10. What are the best equipment management tips for long-term ROI?
Ans. Top equipment management tips include adopting a preventive maintenance schedule, tracking usage trends, analyzing total cost of ownership, integrating data analytics and choosing scalable software. These practices enhance both productivity and profitability.