Technology Trends
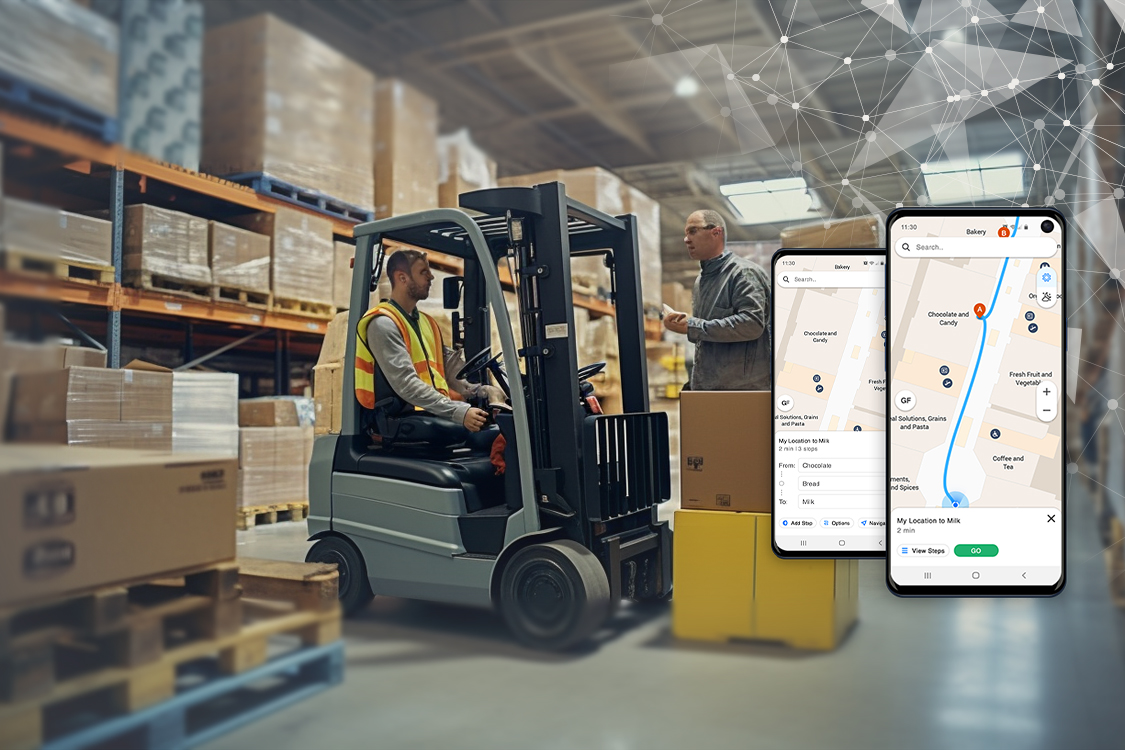
Are you struggling to efficiently handle your customers’ purchase orders because of a cluttered warehouse layout? Do your warehouse staff members encounter challenges in tracking inventory to fulfill sales orders promptly? Is your warehouse compliant with occupational health and safety guidelines? If even one of these scenarios resonates with you, reconsidering your warehouse location mapping strategy could be the transformative decision leading to elevated profits, enhanced efficiencies and exemplary health and safety standards.
This is where an ideal warehouse location mapping strategy can help your warehouse staff streamline operational efforts, reduce life-threatening accidents, as well as win over your customers’ hearts.
The Latest Warehouse Mishaps That You Need To Know
According to a search on the Occupational Safety and Health Administration website, here are just a small section of accidents logged in the past two year:


- An employee is killed when crushed by a bale.
- Employee dies after falling from a box truck.
- Employee dies while loading a truck with a forklift.
- An employee is killed due to heat and carbon monoxide exposure.
- Employee is killed when caught between a forklift and a rack.
Furthermore, approximately three million workers die due to work-related accidents and diseases, and work accidents account for an additional 330,000 deaths, according to a recent analysis by the International Labour Organization. More men die (51.4 per 100,000 working-age adults) compared to women (17.2 per 100,000 working-age adults) due to work-related incidents. Asia and Pacific regions account for the highest work-related mortality (63 per cent of the global labour force), the IOL analysis stated.
10 Factors To Keep in Mind in Your Warehouse Location Mapping Strategy
Below are 10 factors that might be impeding an effective warehouse layout management strategy, along with the corresponding solutions
1. Inappropriate Warehouse Traffic Management
Scenario: At your busy distribution centre, narrow lanes can result in congestion, which can harm forklifters and other warehouse staff members. Just imagine, a forklifter who has to carry a heavy load and pass by a narrow aisle could bump into pedestrians, which goes against occupational health and safety measures and could lead to life-threatening situations.
Solution: Offering dedicated pathways and wider aisles for forklifters can significantly reduce traffic collisions and ensure compliance with safety guidelines.
2. Absence of Signage and Visual Communication
Scenario: There have been increasing incidents of warehouse staff members entering hazardous material storage areas, which can lead to dangerous incidents and warehouse diseases, due to lack of clear signages and wayfinding capabilities.
Solution: Offering clear signage about inventory areas, restricted areas and even emergency exits across your warehouse location can help you prevent dangerous accidents and reduce on-site navigation confusion too.
3. Lack of Designated Walkways
Scenario:Your staff members collide with moving machines within the warehouse, creating a very unsafe environment.
Solution: A dedicated walkway only for pedestrians can help them navigate safely and eliminate the risk of pedestrian-machinery conflicts at the warehouse.
4. Inadequate Wayfinding Capabilities
Scenario: Your warehouse workers spend more time accessing or reaching inventory to fulfill orders.
Solution: Integrating a SaaS-based warehouse mapping tool into your existing warehouse management practice will help your staff members confidently gain access to digital signage and seamlessly navigate through inventory areas, from the tip of their finger.
5. Warehouse Blind Spots
Scenario: Warehouses, often expansive and cavernous, serve as storage spaces for goods. However, poorly lit areas can lead to collisions between workers and the goods stocked. And, even worse with moving machinery too.
Solution: Installing convex mirrors in blind spot areas and appropriate lighting across the warehouse will help your warehouse staff members reduce the chances of accidents and improve worker safety.
6. Unclear Emergency Pathways
Scenario: Your warehouse staff member struggles to locate pathways and exits during unforeseen events like fire outbreaks or earthquakes.
Solution: Conducting frequent drills and allowing staff members to navigate the warehouse through a warehouse location mapping tool that offers digital signages and pathways will help.
7. Unsafe Machinery Operations
Scenario: Improper handling of pallet jacks can result in tipping incidents, posing a risk to nearby warehouse staff. Such occurrences are best avoided to ensure a safe working environment in the warehouse.
Solution: Proper training, especially for inexperienced warehouse staff members can reduce the risk of machinery operations manhandling and material handling mishaps. In addition, comprehensive sessions on equipment operation and ergonomic practices can significantly reduce accidents in the warehouse.
8. Faulty Warehouse Area Risk Assessment
Scenario: Multiple types of products in different sizes stocked at different areas of the warehouse in an unorganized manner can lead to slip hazards and fatal injuries for workers on site.
Solution: A regular risk assessment of warehouse areas will help you identify triggering hazards and ensure timely actions to prevent fatal accidents in the warehouse.
9. Assessment of Safety Protocols
Scenario: A warehouse will introduce potential hazards with time, hence you would like to ensure that they are addressed as per the existing safety protocols.
Solution: Constant risk assessments of safety protocols can ensure that emerging hazards are monitored and addressed on the go.
10. Persistent Improvement of Safety Protocols
Scenario: Despite constant assessment of safety protocols, a recent near-miss incident in your warehouse will lead to a review of the existing protocol.
Solution: Post-incident reviews can lead to improvements in safety measures, eliminating the chances of the same incident in the future.
Closing Note
Adopting an effective warehouse location mapping strategy is crucial for any logistics and supply chain business to ensure the utmost warehouse operational efficiency and safety of warehouse staff. The solutions highlighted throughout the article will address key warehouse mishaps including:
- Managing traffic congestion and
- Machinery operations and material handling hazards.
Therefore, as a warehouse owner or staff member, you will be able to easily mitigate risks while creating a safer working environment by implementing solutions like dedicated pathways, digital signages, wayfinding technology, comprehensive training sessions, regular risk assessments and constant improvements on warehouse safety protocols.
As technology continues to advance, integrating a warehouse mapping tool into existing warehouse practice management systems will offer a centralized solution to boost wayfinding capabilities and emergency preparedness. By adopting warehouse location mapping solutions, warehouse managers and staff can streamline operations, and improve the overall efficiency and safety of a warehouse.
Want to enhance your warehouse location mapping capabilities? Connect with our experts now!
Frequently Asked Questions
Q1. What does the warehouse location mapping tool mean?
Ans. Warehouse location mapping tool helps warehouse supervisors, logistics managers and supply chain business owners to adopt a digitized location mapping solution in the warehouse. Based on your warehouse location heatmaps, the technology offers interactive navigation, wayfinding capabilities, visual communication and real-time analytics.
Q2. What are the key three factors to consider in your warehouse location mapping?
Ans. Location mapping in warehouses can be determined as per several factors, however, inappropriate warehouse traffic management, absence of signages and visual communication and lack of designated walkways are the key three factors that you need to consider in your warehouse location mapping.
Q3. What is the latest technology available for efficient warehouse location mapping capabilities?
Ans. SaaS-based technology built on machine learning protocols is the latest technology available for effective warehouse location mapping capabilities.
Q4. What is the role of digital signage in warehouse location mapping?
Ans. Digital signages are modern types of signages available within the warehouse location mapping solution. This can be created and edited for better optimization in warehouse management.
Q5. What are the five key areas of a warehouse?
Ans. The five key areas of a warehouse are as below:
- Docks area (Loading and unloading of goods)
- Receiving and staging area (Quality control, inventory recording and product inspection)
- Storage area (Warehouse)
- Picking area (Warehouse)
- Shipping area
.